European roll out for Bazooka brand FSDUs
Our high impact FSDU for Juicy Drop Pop range can now be seen in stores across Europe
As long ago as 2020 we detailed a challenging but exciting FSDU project for international confectionery brand Bazooka Candy Brands. The stunning 2m unit reflected the quirky colourful pack design of the Juicy Drop Pop Candy range and supported the brand’s “edible entertainment” philosophy with its funky features and clever & engaging design.
The initial roll out saw the units distributed to resellers throughout Asia, and its success has led to a second reiteration. Over 500 FSDUs for two popular sweet ranges will now be distributed throughout Europe.
From design to distribution
The production process showcased our core plastic fabrication skills. The 540mm base was vacuum formed and manufacturing the components involved line bending, plastic laser cutting and drape moulding processes. We have the skills and leading-edge kit to ensure every part was made with maximum efficiency – minimising material waste and energy use. Precision was essential to ensure the 1.9m high unit could be safely and speedily assembled instore.
Keeping all processes in-house also reduced carbon footprint of the project – as well as delivering cost and project management benefits for the client.
Our near-photographic image quality and text-perfect Océ Arizona printers meant the digitally printed POS more than matched the products zingy ‘popping’ colours and product images.
Unmissable Gravity Fed FSDU for Push Pop Range
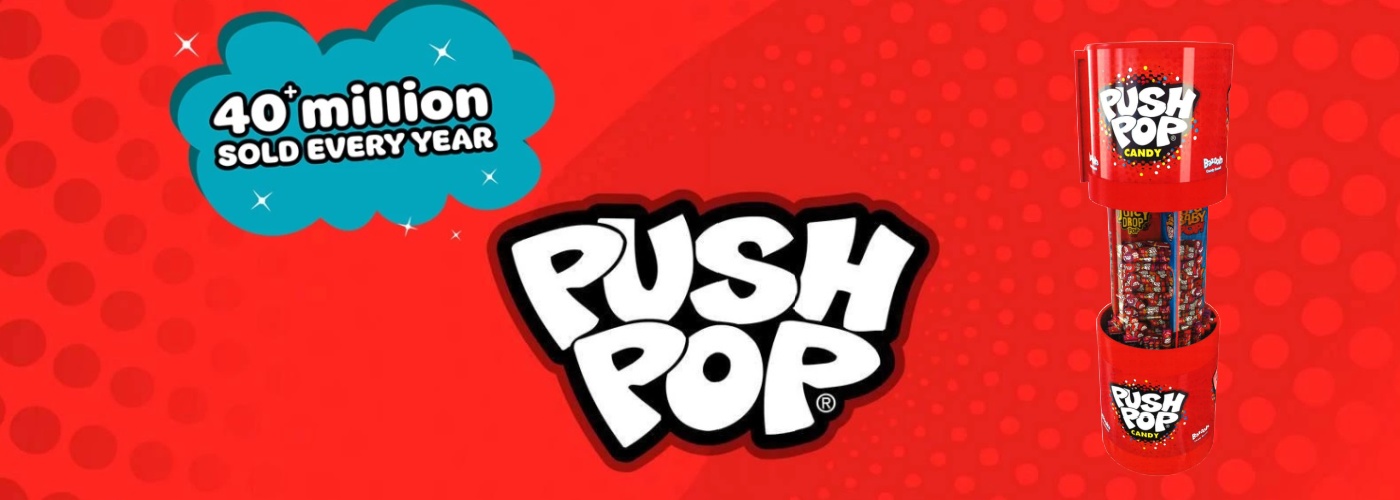
A further FSDU has been developed and manufactured by us and this is also inlcuded in the European rollout. An ‘in yer face’ 1,5m high gravity fed FSDU promotes, displays and dispenses the hugely popular Push Pop hard candy range.
Again with its funky design, acid colours and fun-functionality the stand enhances the brand.
The manufacturing involved the same processes and finishes as the Juicy Drop display unit, and both units are assembed by us and passed to our logisitics team to ensure they arrive – safe, sound and on time – across 100s of European destinations.