Thermoforming is a manufacturing process that involves heating a thermoplastic sheet until it becomes pliable and then shaping it into a desired form using a mold or a tool. The process involves heating the sheet until it reaches its forming temperature, typically between 300°F and 400°F, and then using pressure or vacuum to mold it into the desired shape.
There are several types of thermoforming processes, including vacuum forming, pressure forming, drape moulding and twin sheet forming. Vacuum forming involves using a vacuum to draw the heated sheet into the mold, while pressure forming uses a combination of vacuum and pressure to create more intricate and detailed parts. Twin sheet forming is a process in which two sheets are heated and molded simultaneously to create a hollow part with two separate walls.
Thermoforming is commonly used in the production of packaging, automotive parts, medical devices, and consumer goods, among other applications. It is a popular alternative to other manufacturing processes, such as injection molding, due to its lower tooling costs and ability to produce complex shapes with varying wall thicknesses.
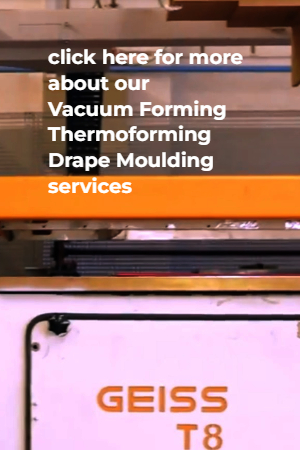
Is thermoforming expensive?
The cost of thermoforming can vary depending on several factors, such as the size and complexity of the part, the type of material being used, and the production volume.
In general, thermoforming is considered a cost-effective alternative to other manufacturing processes, such as injection molding or machining, for producing plastic parts. The tooling costs for thermoforming are typically lower than for injection molding, making it a more affordable option for small to medium production runs. Additionally, the speed and efficiency of the thermoforming process can result in reduced labor costs compared to other manufacturing methods.
However, it’s important to note that the cost of thermoforming can increase for parts that require intricate designs, tight tolerances, or specialised materials. The cost of the raw material can also affect the overall cost of thermoforming, as some materials may be more expensive than others.
Overall, thermoforming can be a cost-effective manufacturing process for producing plastic parts, especially for smaller production runs or parts with less complex designs.
Is thermoforming sustainable?
Thermoforming can be a sustainable manufacturing process when used appropriately. Here are some factors that can make thermoforming a sustainable option:
- Material selection: The choice of material can significantly impact the sustainability of thermoforming. Using recyclable or biodegradable materials, such as recycled PET, bioplastics or paper-based materials, can help reduce the environmental impact of the manufacturing process.
- Energy efficiency: Thermoforming can be an energy-efficient process when the equipment is designed to minimise energy consumption. For instance, using energy-efficient heaters and controlling the temperature of the heating elements can help reduce energy use.
- Waste reduction: Thermoforming can help reduce waste by using the minimum amount of material required for the part and by using scrap material for other purposes. Additionally, thermoforming can be designed to produce parts that are easily recyclable at the end of their life.
- Transportation: Thermoforming is a lightweight process, and the parts produced can be stacked and nested to minimise the transportation footprint. This can help reduce the overall carbon footprint of the manufacturing process.
Overall, thermoforming can be a sustainable manufacturing process when used in conjunction with sustainable materials and practices. However, it’s important to note that like any manufacturing process, thermoforming can have environmental impacts, and it’s essential to take steps to minimise those impacts.
A brief history of thermoforming
Thermoforming has a rich history that dates back over a century. Here is a brief overview of the key milestones in the development of thermoforming:
- 1890s: The first patent for a thermoforming process was filed by Edwin Ruud, who developed a method for forming sheet metal using heat and pressure.
- 1930s: The first plastic thermoforming process was developed, using a heat lamp to soften the plastic sheet and then pressing it into a mold.
- 1940s: Thermoforming gained popularity during World War II as a way to produce lightweight and durable components for aircraft and military vehicles.
- 1950s: The first continuous roll-fed thermoforming machines were developed, allowing for high-volume production of plastic parts.
- 1960s: Thermoforming expanded into new industries, including automotive, appliance, and packaging.
- 1970s: Advances in material technology and machinery allowed for the production of more complex parts with tighter tolerances.
- 1980s: The introduction of computer-aided design (CAD) and computer-aided manufacturing (CAM) allowed for greater precision and efficiency in the thermoforming process.
- 1990s and beyond: Thermoforming continues to evolve, with new technologies and materials being developed to improve efficiency, reduce waste, and increase sustainability.
Today, thermoforming is a widely used manufacturing process with applications in a variety of industries, including packaging, automotive, medical, and consumer goods. The process has come a long way since its early days, and continues to be an important part of the plastics industry.
Recent Comments